Im oberen Stollensystem sollte, wie auch im
unteren System, ein Presswerk der Ambi-Budd aus Berlin
untergebracht werden. Nachdem die Pressen bereits
montiert waren, erging jedoch die Weisung, die
installierten Maschinen wieder zu demontieren, da den
neuen Anweisungen zufolge nun eine
Fabrikationseinrichtung für Elektronenröhren der
Philips-Werke untergebracht werden sollte. Da die
bisherigen elektrischen und baulichen Gegebenheiten
nicht erfüllt waren um diese Fabrik betreiben zu können,
mußten umfangreiche bauliche Veränderungen, sowie
zusätzliche Pressluft- und Gasversorgungen
sichergestellt werden. |
|
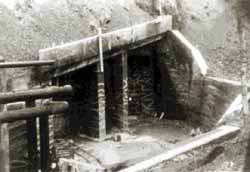 | |
Vor allem, da die Produktion das Vorhandensein
von Wasserstoff, Stickstoff und Vakuumpumpen erforderte.
Aus Platzgründen wurde die erforderliche Heizung in Form
eines, vorerst provisorischen, Kesselhauses vor der
Einfahrt des unteren Stollensystems eingerichtet.Die
Gasversorgung erfolgte durch das öffentliche
Gasverteilernetz der Ruhrgas A.G. Zur Sicherstellung der
Wasserversorgung sah man ein Wasserwerk an der Weser
vor, die Entwässerung sollte durch Rohrleitungen der
Weser zugeleitet werden. Diese Rohrleitung verlief
zusammen mit den anderen erforderlichen Leitungen durch
einen dafür vorgesehenen Versorgungsschacht. Alle
erforderlichen Umbau- und Zusatz- arbeiten nahmen die
Zeit bis Januar 1945 in Anspruch. |
|
Foto : Der Hauptzugang zur Anlage
Stöhr
I | | |
Zusätzlich zu den Philips-Werken wurde in
dieser Anlage noch eine weitere Produktionsfirma
untergebracht, die Ihre Produktion bereits Ende August
1944 aufgenommen hatte. Die Firma Rentrup aus Stadthagen
fertigte Spulen aus isoliertem Stahldraht. Die
Verwendung dieser Spulen ist bisher nicht
bekannt.
Die Energieversorgung der Anlage erfolgete wie
im unteren Stollensystem durch eine 25 kV
Hochspannungsleitung, jedoch banden sich die zugehörigen
Transformatoren im unteren Stollensystem. Hie auf 220
bzw. 380 V herabtransformierte Spannung wurde dann durch
eine Entsprechende Leitung in das obere Stollensystem
geleitet. |
|
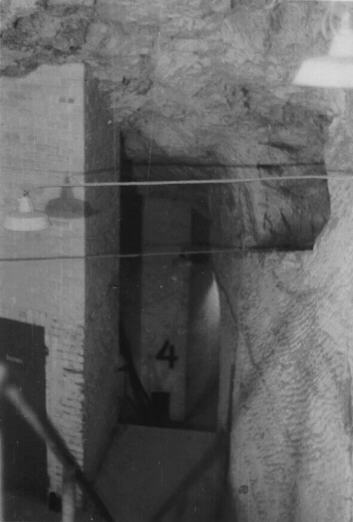 | |
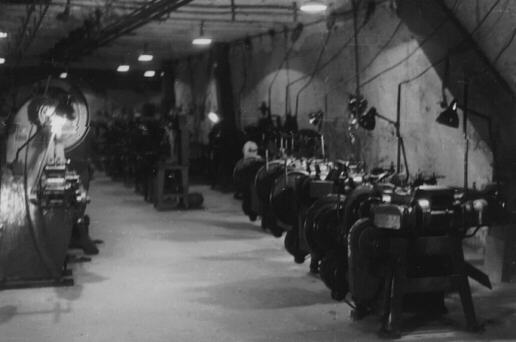
|
Die Produktion der Philips-Werke
wurde auf mehrere Etagen verteilt. Durch das Einziehen
entsprechender Zwischendecken wurden insgesamt zehn
Etagen geschaffen, von denen die oberen zwei
wahrscheinlich zur Unterbringung eines Lüftungssystems
dienten. |
|
Fotos : Oben - Treppenhaus zwischen
den Etagen / Unten : Bestückte
Maschinenhalle | | |
|
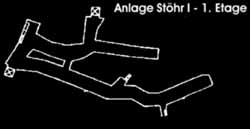
|
Die erste Etage der Anlage beherbergte das
Maschinenhaus und die notwendigen Werkstätten zur
Instandhaltung und zum Betrieb der Anlage.Hier waren die
Kompressoren für Pressluftanlage, sowie die Tanks und
Kompressoren für die benötigten Gase, wie z.B.
Wasserstoff und Stickstoff untergebracht. Außerdem
standen hier die für den Produktionsbetrieb notwendigen
Vakuum-Pumpen. Die erste Etage umfasste eine Fläche von
1.003 Quadratmetern. |
|
|
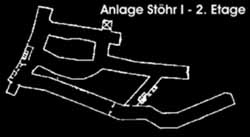 |
In der zweiten Etage waren die
Fertigungsabteilung für die Unterteile und die
Produktion der Elektronengitter untergebracht.Hier
wurden neben den Elektronengittern die Röhrensockel
gefertigt, mit denen die Röhren später in die
entsprechenden Geräte eingesteckt oder eingelötet werden
konnten.Die zweite Etage umfasste eine Fläche von 1.109
Quadratmetern. |
| | |
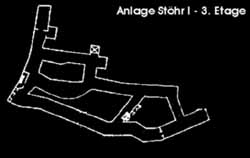
|
Auf der dritten Abteilung befanden sich die
Fertigung der Glaselemente, sowie die Abteilung für die
Materialprüfung. Hier wurden die einzelnen, produzierten
Komponenten der Elektronenröhren überprüft. Außerdem
wurden hier die Glaskuppeln für die Röhren hergestellt.
Die dritte Etage umfasste eine Fläche von 1.507
Quadratmetern.
|
|
|
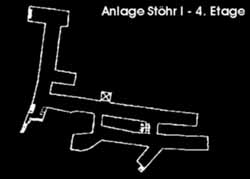 |
Auf dieser Etage befand sich die Einrichtung
für die Endmontage der Röhren. Die einzelnen Komponenten
wurden hier zu den fertigen Elektronenröhren
zusammengesetzt.
Die vierte Etage umfasste eine Fläche von 925
Quadratmetern. |
| | |
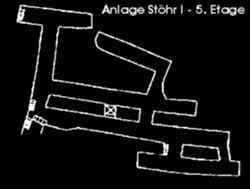
|
Die fünfte Etage diente ebenfalls für die
Endmontage. Wahrscheinlich wurden die Röhren auf den
zwei entsprechenden Etagen in zwei Stufen
endmontiert.
Die fünfte Etage umfasste eine Fläche von
1.473 Quadratmetern.
|
|
|
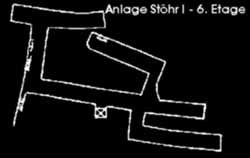 |
In der sechsten Etage befand sich die
Abteilung für die Endprüfung der produzierten Röhren.
Hier wurde die Produktionsqualität überwacht und
eventuelle Mängel weitergeleitet.
Die sechste Etage umfasste eine Fläche von
1.119 Quadratmetern. |
| | |
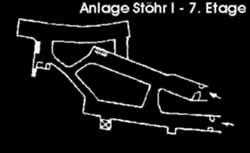
|
Die siebte Etage beherbergte die
Versandabteilung. Hier wurden die produzierten Röhren
verpackt und an die betreffenden Versandwege wie z.B.
Bahn oder LKW weitergeleitet. Neben der Versandabteilung
war auf dieser Etage auch das Labor der Anlage
untergebracht. Seine Aufgabe war es unter anderem, neue
Produkte zu entwickeln und vorhandene Mängel zu
beseitigen. Die siebte Etage umfasste eine Fläche von
1.079 Quadratmetern. |
|
|
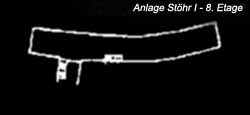 |
In der achten Etage befand sich eine weitere
Abteilung zur Komponentenfertigung. Hier wurden die
Kathodenelemente für die Röhren
produziert.
Die achte Etage umfasste eine Fläche von 100
Quadratmetern. |
| | |
Nach Ende des Krieges wurde auch diese Anlage von
den Alliierten eingenommen und gründlich untersucht.
Anschließend erfolge die Demontage der
Produktionsmaschinen. Später wurde dann die gesamte Anlage mit
Sprengstoff versehen und im Inneren sämtliche
Zwischendecken und Tunnel zum Einsturz gebracht.Zu
diesem Zeitpunkt war die Anlage durch den Haupteingang
noch eine Zeit lang zugänglich. In den 70ern versuchte
man kurzfristig eine kommerzielle Nutzung der Anlage zu
realisieren. |
|
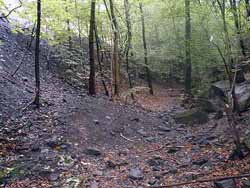 | |
Zu diesem Zweck richtete man für einige Jahre
eine Champignonfarm innerhalb der noch zugänglichen
Bereiche ein, die aber später wieder entfernt wurde.
Wahrscheinlich geschah dies unter anderem aus
Sicherheitsgründen.Die vorhandenen Lüftungsschächte
wurden dann mit Beton vergossen. Beim Hauptzugang, wurde
erst der eigentliche Zugang zur Anlage gesprengt,
anschließend die den Eingang umgebenden Betonbauten.
Dies geschah bereits in den frühen 80ern. Die gesamte
Anlage wurde auf diese Weise hermetisch verschlossen, so
dass in heutiger Zeit keine Zugangsmöglichkeit mehr
besteht und nur noch einige große Betonbrocken an die
ehemalige Anlage erinnern. |
|
Foto : Nur noch die Schneise im
Wald lässt eine ehemalige Zufahrt
vermuten. | | |
|